Cosmic Color Ribbon (CCR) arches are a colorful addition to a Light-O-Rama (LOR) Christmas light show. I have six of them in this year’s Christmas show. The smaller size of my yard makes it more practical
to scale down the size of the arches. So I make two smaller arches out of one CCR.
WARNING: Following these instructions will violate the warranty on your CCR. Do not use these instructions if maintaining the
warranty on your CCR is important to you. I cannot accept responsibility for damage done to your CCR as a result of following these instructions and LOR will not replace a CCR that you’ve damaged by cutting
it. Some of the steps provided require a proficiency in soldering and some basic understanding of electronics and electrical wiring. If you’re not comfortable with soldering don’t try to learn on a CCR!
Have your electronics savvy friend help out.
I am so concerned about the many ways to damage a CCR that I repeat the warnings of what not to do in this illustrated guide. I hope you don’t mind. I don’t want you to tell me I didn’t warn you. With
the requisite disclaimer out of the way, the following illustrated instructions is how I build my half sized arches. I recommend that you read this entire guide before you decide if making arches this
way is what you really want to do.
I’m an RF engineer with soldering certification so I may make soldering look easier than it may be for the average person. If it’s been a while since you soldered, I recommend that you practice soldering
some wires together or whatnot for practice before you cut loose (no pun intended) on your CCR. If you need a good primer on how to solder, I recommend you read this fairly well written instructable:
http://www.instructables.com/id/How-to-solder/
I intended this guide to be very detailed and well illustrated. If you feel I left something out or didn’t explain something in a clear way, please message me on the LOR forum and I’ll update the guide.
Step 1 - Testing your CCR
Before you begin violating the warranty on your CCR, it is important to make sure it works properly while still in a condition to be exchanged under warranty. I created a sequence in Showtime S3 that
sequences the ribbon through many different colors, slow fades, and patterns.
Connect up the power supply, controller, and CCR and let it run for at least 24 hours. This is called “burn-in” and is premised upon the fact that most electronic failures due to a defect in an integrated
circuit, circuit board, or tri-color LED will occur within the first few hours of use. That is not to say it can’t happen later but internal defects in electronic components usually cause a failure of
the device sooner rather than later.
Step 2 - Making the PVC Frame for the Arches.
Parts required: 2 x 10 foot “schedule 40” ¾ inch black or gray PVC. You should be able to find it in the electrical section of your local hardware store.
I purchased a 4’ x 8’ ply-board to create a frame to bend the PVC on to form arches. Each CCR will make two arches 62 inches wide and 31 inches tall (radius) with a circumference of 98.5 inches. I add
an additional two inches to keep the ends of the CCR two inches off the ground or snow. Thus, I cut each PVC to 102.5 inches. But, I hold of on cutting until after the arches are bent. Using a marker,
I mark the cut point before bending (it’s harder to measure the cut point after the arch is bent).
On the ply-board, I place a single screw at dead center at 2 inches up from the bottom edge of the board. I then use a tape measure to mark a 31 inch radius arc on the board with a pencil. Using a screw
gun, I screw in a 1½” screw every inch along the arc. This is the form I will use to bend and set the PVC. See Figure 1.
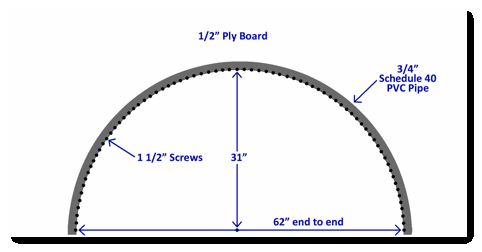
Figure 1 - Ply Board Form
I use a gas BBQ grill with the rotisserie hardware removed. That leave two holes at each end of the grill with the lid closed that are perfect for pulling the PVC through to heat it. I set my BBQ on a
medium flame. I wear leather gloves as the PVC can get hot enough to burn your hands. I slowly draw the PVC through back and forth several times through the grill until the PVC becomes pliable. Make sure
the ends of the PVC are also pliable (I’ve made the mistake of not getting the ends hot enough to bend).
Once the PVC is pliable, as quickly as possible, place it on your mold and bend it around the arc leaving one end even with the end of the ply board and the other end with the cut mark extending beyond
the end of the ply board. The PVC should be pliable enough to make the bend without trying to spring back. Let it sit and cool for 15 minutes. Then repeat the above for your second arch. After both arches
have cooled, then cut them to proper length at the cut point you marked earlier.
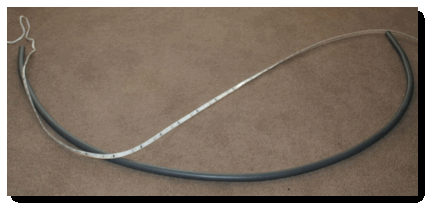
Figure 2 - The Bent PVC Pipe
I forgot to take a photograph of the PVC on the form but Figure 2 above gives you a good idea of what it looks like prior to mounting the CCR on it. More on that later.
Step 3 - Cutting the CCR
It is in this step that you violate the warranty of your CCR. I strongly advise that you read the entire instructions below before
you begin this step. Make sure that you are confident of the skills required to complete the project before committing to this step.
Locate the 25th cut point along the ribbon. Measure the ribbon’s entire length. It should be 197 inches long, +/- 1 inch. The center should be the cut point at around 98 inches. Both count and measure
as once you cut the ribbon, you can’t easily fix the mistake of cutting it in the wrong place. Typically, that cut point has soldered bridges on it. Mark that cut point with a magic marker.
Using an x-acto precision knife gently cut the UV resistant weather seal tube as shown in Figures 3, 4, and 5. Make absolutely
sure that the CCR is not plugged into the controller.
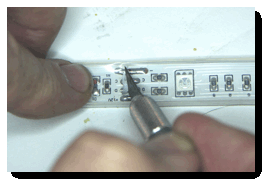
Figure 3
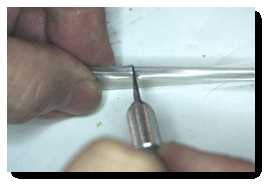
Figure 4
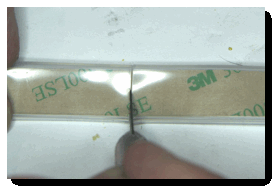
Figure 5
Now gently pull both sides of the tube to expose the cut point as in Figure 6. Turn the ribbon over and lightly score the paper backing with your x-acto knife.
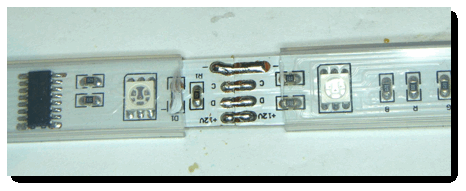
Figure 6 - Exposing the Cut Point
Using a low temperature grounded tip soldering iron, remove the wire bridges at the cut point. If you have a soldering iron where you can set the temperature, set it to no higher than 325C (600F). If
the temperature cannot be adjusted, use a pencil tip soldering iron of between 25 and 40 Watts. DO NOT use a soldering gun. They get too hot and will damage the delicate circuit board traces.
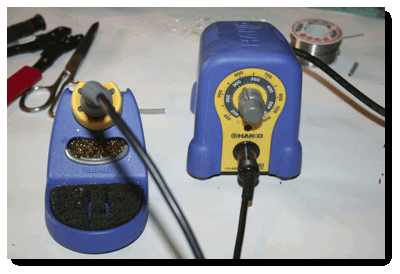
Figure 7 - My Temperature Controlled Soldering Station.
Note the Temperature Setting (325C / 600F).
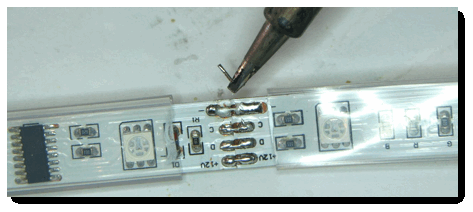
Figure 8 - Removing the Wire Bridges
Now, using solder wick or a solder vacuum, remove the excess solder from the cut points so there is no solder bridge between them as shown in Figure 9. Here, I’m using solder wick.
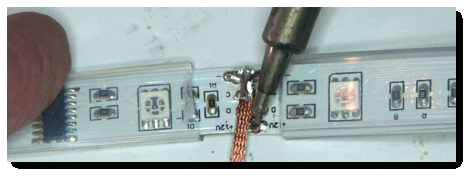
Figure 9 - Remove Excess Solder with Solder Wick or Solder Vacuum
With no solder bridges remaining between both sides of the cut point, you may now gently separate the CCR into two ribbons.
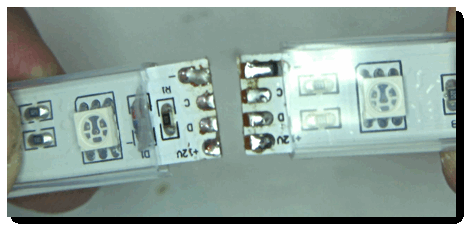
Figure 10 - Separating the CCR
Set the two halves of the CCR aside for now. It’s time to build the interconnecting cable.
Step 4 - Building the Interconnect Cables
For flexibility, I designed a cable system that allows me to connect two arches close to each other or separate them by up to 25 feet by using an extension cable.
The interconnect cable consists of a short 6 inch cable and Molex connector on each end of the ribbon and a 24’ extension cable. If you don’t anticipate a need to separate the arches then you can forego
the building of the extension cable. I’ll provide instructions on it anyway just in case.
Purchase a 25’ 22 gauge stranded four conductor cable. Most any electronic store, including Radio Shack, should carry the cable.
Cut two 6 inch sections. These will be the short connector cables attached to the ribbons. Set aside the remaining 24’ cable. Remove approximately one (1) inch of insulation from the short cables as shown
in Figure 11. If you’re going to build a 24’ extension cable, do the same to it.
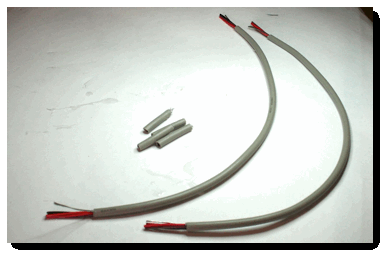
Figure 11 - Two 6” Cables for Cable Ends of CCR
Strip a small amount of insulation off of each individual wire as shown in Figure 12. Do this for both ends of the two short cables. If you’re going to build the 24’ extension cable do the same with it.
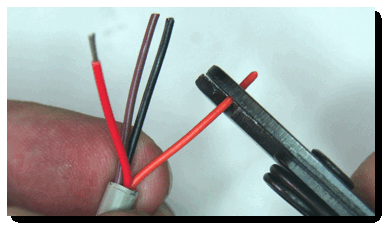
Figure 12 - Stripping Insulation from Individual Wires
When you’re finished stripping the wires, it will look something like this:
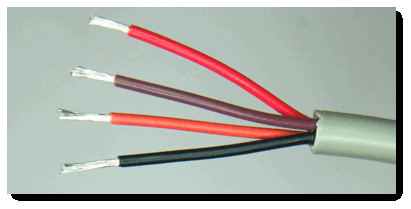
Figure 13 - All Four Conductors Stripped
At this point we need to give some thought to how things work with the CCR and controller because we want to make sure to put the right gender Molex connector on the correct half of the CCR. I use a basic
rule of thumb - female connectors attach towards the controller. Male connectors attach towards the end of the CCR. In fact, before I start to assemble anything, I write down notes that I can use to double
check the plan as I work. Figure 14 is the note I wrote to follow.
Figure 14 - Make A Plan and Write It Down
Referring back to Figure 6, you’ll notice that I assigned conductor colors to the traces on the circuit board. The figure is upside down but you’ll see what I’m doing here. On the ribbon circuit traces,
+12V carries the +12 Volts DC supply. The trace marked “D” is the data circuit. The trace marked “C” is the clock circuit, and the trace marked “-” is the -12 Volts DC supply.
It is absolutely imperative that you do not mix up your colors else permanent damage will be done to the CCR when it is powered up.
Here, I’ve also assigned the colors for the connectors for the pinouts for the Molex connectors. The colors of the conductors in your cable may be different. You may need to account for that. I’ve also
written down that the female Molex connector is attached to the half CCR that attaches to the supply (controller). That’s the half with the white cable that attaches to the controller. More on that in
a bit.
Here’s the Molex connectors I use for the project:
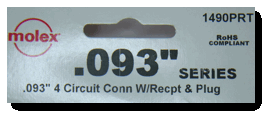
Figure 15 - A Package of Two Male and Two Female .093” Molex Connectors
Remove a male and a female Molex connector shell from the package. Also remove four male and four female crimp pins.
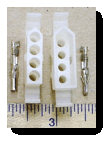
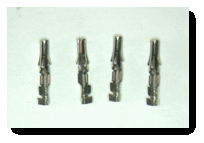
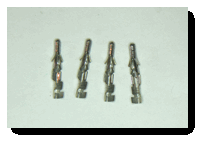
Figure 16 - From Left to Right - Female Shell, Male Shell, Female Pins, Male Pins
Note that there is a “V” shaped end to both the female and male Molex shells. This denotes pin #1 as referred to in the bottom half of my notes in Figure 14.
Using a crimp tool, on one short cable, crimp four female pins to the conductors. On the other cable, crimp the male connectors as shown in figures 16 and 17.

Figure 16 - Crimping the Molex Pins to the Conductors
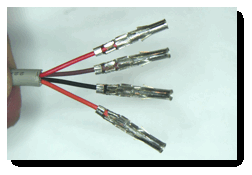
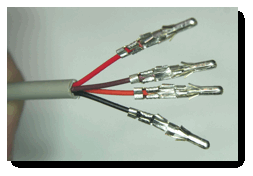
Figure 17 - Left to Right - Female Pins and Male Pins Now Crimped
Since the CCR arches will be operated outdoors, the wires will need to be soldered to prevent corrosion should moisture get inside the connectors.
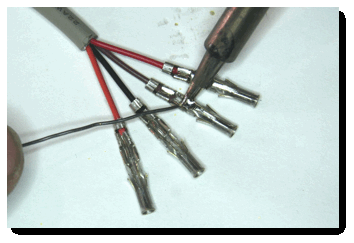
Figure 18 - Soldering the Molex Pins
When you’re finished soldering the pins, they should look something like this. Again, it is important to not use a soldering iron that is too hot least you’ll melt the insulation.
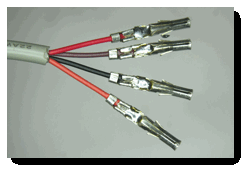
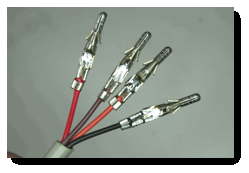
Figure 19 - Left to Right - Soldered Female and Male Molex Pins
At this point, you should have two 6” cables. One with female Molex pins on it and the other with male Molex pins on it. Lets now insert the pins into the shells. First, we’ll insert the female pins into
the female shell. Make sure you observe the color codes. Again, the “V” end denotes pin 1.
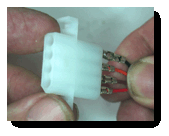
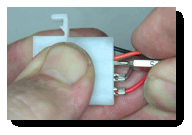
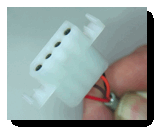
Figure 20 - Assembling the Female Molex Shell
You can see in the above images that my red conductor is pin 1, brown is pin 2, orange is pin 3 and black is pin 4. I’m using a jeweler’s screwdriver to push the pins all the way in until they lock (as
can be determined when you hear the click).
Now insert the male pins into the male shell.
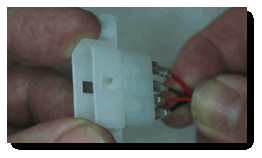
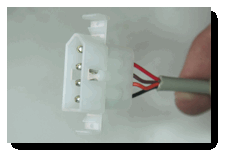
Figure 21 - Assembling the Male Molex Shell
Having worked in electronics for many years, one thing I’ve always done with cables and connectors is to create strain relief. This prevents the conductors from breaking if flexed too much. This is a
step you can add or skip. Personally I recommend adding strain relief.
I use heat shrink tubing. Select a diameter of heat shrink tubing slightly larger than your four conductor cable. Then cut four pieces approximately an inch and a half long. Slide two heat shrink tubes
onto each of the two short cables from the end without the molex connector as shown:
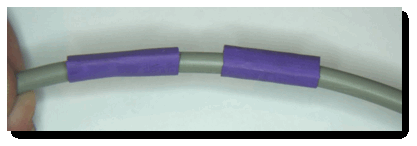
Figure 22 - Two Heat Shrink Tubes
Slide one of the heat shrink tubes as far as possible over the small conductors leading into the Molex connector.
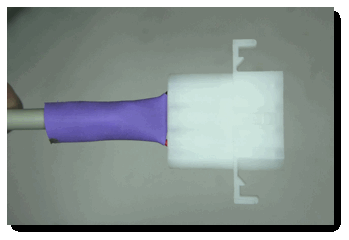
Figure 23 - Heat Shrink Tube Pushed Towards Molex Connector
Using a cigarette lighter or heat gun, shrink the tubing around the cable. I just use a lighter. Be careful to not over-heat the tubing. It can catch flame or split. Heat it just enough on both sides
that it shrinks. Hint - if you’re using a lighter, it is better to heat the shrink tubing in the blue part of the flame. If you heat it above the top of the flame, it will leave carbon deposits on the
tubing.
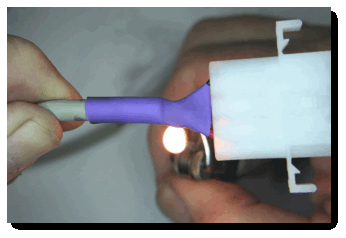
Figure 24 - Shrinking the Heat Shrink Tube
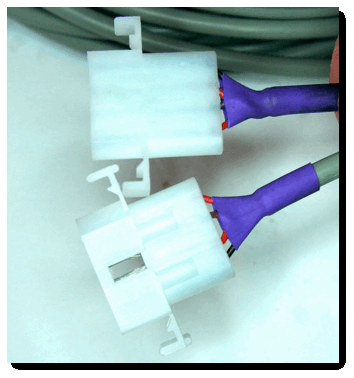
Figure 25 - Both Female and Male Molex Connectors Assembled with Strain Relief
Step 5 - Attaching the Interconnect Cables to the CCR
Now that the interconnecting cables are built, it’s time to attach them to the two halves of the CCR. Remember, the female cable (shown in Figure 20) will attach to the CCR half that has the white cable
that connects to the controller. The male cable (shown in Figure 21) attaches to the other half CCR.
Included inside the box your CCR was packaged in is a small plastic bag of glue and parts.
Figure 26 - Spare Parts Bag Included With CCR
You’ll need the tube of glue and the two end caps with the four holes in them for the next steps.
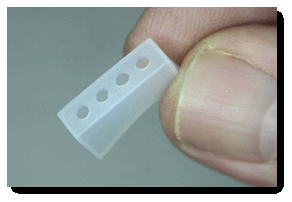
Figure 27 - End Cap
Making sure the second un-shrunk heat shrink tube is still on the cable, insert the wires to be soldered to the CCRs through the end caps as shown below, making sure to arrange the wires according the
the proper color code you’ve determined for your cables. This is a good time to refer to your wiring color code table you made
earlier as getting this step wrong will surely result in permanent damage to the CCR when it is powered up later.
Figure 28 - Wires Inserted Through End Cap
Notice that I pre-tinned (soldered) the wires before this step. This is a common practice in soldering which makes it easier to solder the wires to the circuit trace and reduces the amount of heat that
is transferred to the circuit trace, thereby reducing the likelihood of damaging the circuit trace.
Now solder the wires to the CCR ribbons being very careful to inspect each circuit trace when you’re finished to make sure there are no solder bridges between any of the traces.
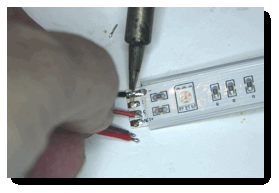
Figure 29 - Soldering the Interconnect Cables to the CCRs.
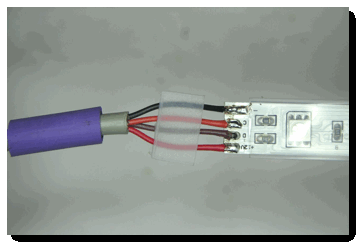
Figure 30 - Check For Solder Bridges and Make Sure The
Color Codes are Correct!
I can’t stress enough that you need to make sure there are no solder bridges between circuit traces and the color code arrangement of the conductors is correct. Forgive my repeating it again but it is
very important to verify and verify again. Okay, I’ll relax.
Now that you’ve soldered the interconnect cables to both CCR halves, using the tube of glue included with your CCR, glue the end cap to the weather resistant rectangular tube. You’ll need to push the
rectangular tube covering the CCR forward to cover over your soldered connections.
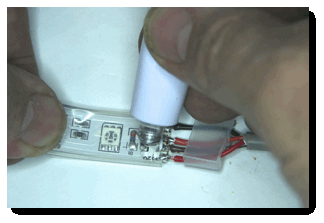
Figure 31 - Run Glue All Around the CCR Rectangular Weather Protection Tube
I prefer to apply the glue to the rectangular weather protection tube on the CCR rather than the end cap. While you’re applying glue, put some directly onto the wires too. That will ensure that the holes
in the end cap are also sealed against weather. Slide the end cap onto the CCR, wipe off excess glue and let the glue set up overnight.
Once the glue has set up properly you can now heat the heat shrink tube to provide strain relief to this end of the cable in the same manner you did with the Molex connectors. Be careful, however, to
not overheat the end cap or CCR itself.
You’re done splitting the CCR in half and adding interconnect cables. Next, we’re going to attach the CCRs to the PVC arches.
Step 6 - Attaching the CCRs to the PVC Arches
Here, I need to stress several important things to be careful of:
1.
Attaching the CCRs to the PVC creates a situation where, if you’re not paying attention, you can damage the CCR by stepping on it, twisting it, or bending it too much. Per the
instructions in the manual (page 9) the following is stated:
”The ribbon is a flexible circuit board with surface mount components on it. Do not crush or bend it sharply. The ribbon can be made to conform to a 3 foot diameter arc in the plane of the ribbon as opposed to bending it in its long dimension. When bending the ribbon in its plane, there will
be minor buckling and this is ok. Do not attempt to flatten the ribbon completely.
Do not pull on or stretch the ribbon. The ribbon is not meant to be continuously flexed. It should be mounted and then left alone.
When tying the ribbon to a structure such as an arch, put the cable ties or clps at the ‘cut points’ - see Detailed Ribbon Description section. There are no electronic components
at these points. Tighten cable ties only enough to keep the ribbon from moving. Do not distort the rectangular silicone tube too much.”
2.
You need to decide which end of the first arch is where pixel 1 will be mounted. Pixel 1 is the first LED located at the white wires that connect to the controller. Whichever end
of the first arch you work that out to be, make sure that pixel 26 on the second arch starts on the same end of that arch. Pixel 26 is the LED closest to the male interconnect cable connected to that
half of the CCR.
For my arches, pixels 1 and 26 started at
the right hand side of the arch with the arch facing me.
3.
Before you mount your CCRs to the arches, now would be a good time to test them again to make sure all of your wiring and all of the pixels work correctly. It is easier to fix
any problem now than after ribbons are mounted to the PVC arch. First plug the two interconnect cables together, plug the white cable into the unpowered controller, then power up the controller. I use
a set of test patterns, colors, and fades that I created in Showtime S3 to test my arches.
A slow fade up to white with a slow fade
down is probably the best test you can do as white requires that all three primary colors of each tri-color LED turn on at the appropriate luminance. If any surface mount component or LED is damaged,
the pixel will have a color other than white or not turn on at all.
With all of the considerations out of the way, let’s get started with mounting the ribbons to the PVC arches. You’ll need around 60 x 6” white tie wraps as we’ll tie wrap the ribbon to the PVC arch at
each ‘cut point’ along the ribbon.
You’ll remember that I cut my arches to 102.5 inches in length before bending them. That was to allow two inches of extra length on each end of the arch to keep the ribbons off of the ground and so that
the cables attached to the ribbons don’t have to make a sharp bend at the ground surface.
Find yourself a comfortable chair and lay everything out in front of you and get to work. The following photographs show me tie wrapping the ribbons to the PVC arches:
Figure 32 - Tie Wrapping the Ribbon to the Arch.
Make sure to tie wrap only at the cut points!
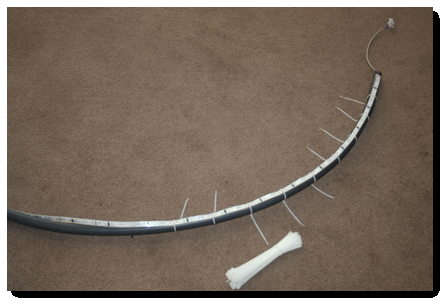
Figure 33 - Working My Way Around
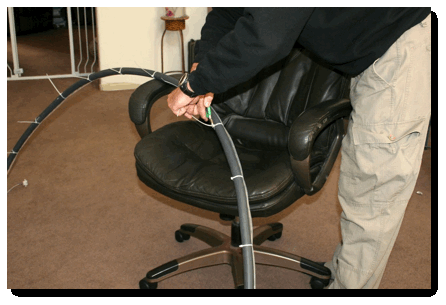
Figure 34 - Cutting the Ends Off of the Tie Wraps
You’ll probably notice a slight discrepancy in the preceding photographs. I’m tie wrapping at every other cut point. I like to do it that way as I will later better secure the ribbon to the arch with
stretch wrap. If there’s any part of the ribbon where I think it needs an additional tie wrap, I’ll add one here and there - always at a cut point.
At this point, if you’ve tie wrapped every cut point you could call it done if you want. I personally like to protect the ribbon better by wrapping the arch with clear stretch wrap. You can buy in the
packing section of most hardware stores.
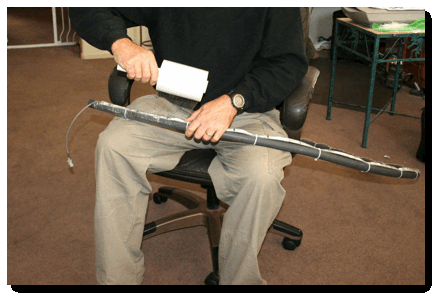
Figure 35 - Protecting the Ribbon (and securing it better) Using Stretch Wrap
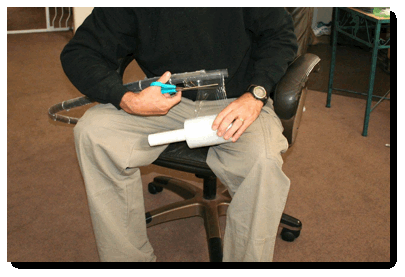
Figure 36 - Finishing Up the Stretch Wrapping
With the stretch wrapping finished, I like to double tie wrap the cables on each end of the arch. I do this to prevent damage to the ribbon if someone trips over a cable and jerks on the arch.
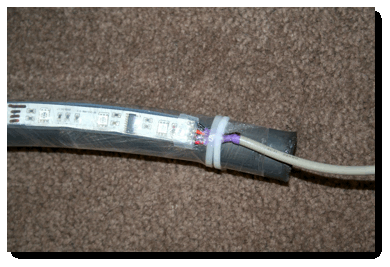
Figure 37 - Double Tie Wrap Your Cables for Added Protection
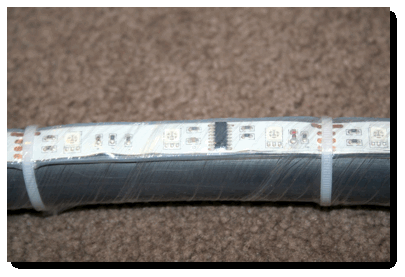
Figure 38 - A Section of the Arch After Tie Wrapping and Stretch Wrapping
Notice in Figure 38 above some slight buckling of the circuit board of the arch. This is okay. Don’t try to flatten it. You’re likely to damage surface mount components by trying to flatten it.
You’re finished!
After I finish mounting the ribbons to the arches I like to test them again.
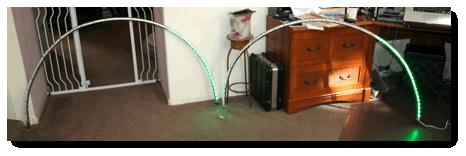
Figure 39 - Testing the Final Product - They Work!
Some Closing Thoughts
It probably goes without saying that when you set up your arches in your light show, be careful to attach them to stands only at the cut points. That, or very loosely so as to not cause damage to the
ribbon.
You may recall that there’s a 24’ piece of cable left over. There’s also a male and female Molex connector and pins left over too. I use that cable to create an extension cable in case I want to separate
the arches by more than a foot. Having the Molex connectors makes it easy to connect the arches directly together or separate them with the extension cable. It’s your choice if you want to go through
the extra work of making the extension cable. If you decide to, follow the same instructions in Step 4.
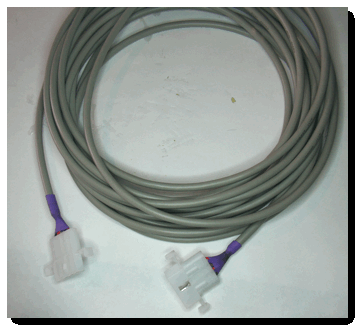
My Completed Extension Cable